
The company is using the platform at its Orlando Innovation Campus (OIC), an R&D facility that is developing new technologies and solutions to address the evolving needs of the energy industry.

In addition, by printing directly to the platform without needed onsite support, users save on material costs and post-process their prints even faster.įor example, Formlabs user Siemens Energy has implemented the Build Platform 2L to print large parts, including molds and manufacturing aids, directly from the platform without onsite support. The Build Platform 2L enables users to more efficiently produce large parts with the same post-processing efficiency Form 3/B/+ users have enjoyed since the launch of the first Build Platform 2 last year, specifying the brand.Īccording to the new product’s description, thanks to its patented Quick Release Technology, users can easily and quickly remove large-format parts from the platform without tools in seconds.
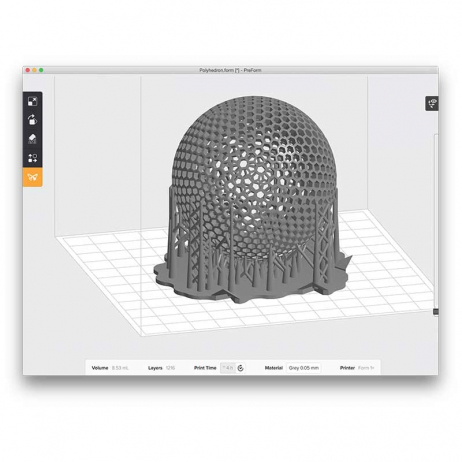
Image courtesy of Formlabs.Īlso being introduced is Build Platform 2L, Formlabs’ next-generation build platform specifically designed for the Form 3L and Form 3BL printers. “With Flame Retardant Resin we can go from CAD design to finished part without the additional work we had to do with other methods.” Formlabs Build Platform 2L. “Being able to get a 3D printed part that truly mimics a thermoplastic, finishes well, has fine feature details, and behaves mechanically similar to molded parts is a huge benefit and time saver,” added Tony Parker, Principal at Avance Design, a 3D printing product design group. It also allows for detailed, high-quality parts with a smooth finish that looks like they were made using injection molding but at a much lower cost. Ideal for making airplane, automobile, and railway interior parts, as well as electronic components and industrial parts, the material eliminates the need for expensive traditional manufacturing methods for making flame retardant parts, ascertains Formlabs.įurthermore, the company established that the resin is certified to have good flame, smoke, and toxicity ratings, which makes it a safe choice for many applications. Image courtesy of Formlabs.įormlabs Chief Product Officer Dávid Lakatos said that with the brand’s first-ever FR Resin, they are opening up 3D printing to industries that must adhere to product regulations and certifications for flame retardancy, particularly aviation and transportation.Īs Formlabs’ first UL (Underwriters Laboratories) 94 V-0 certified resin and first self-extinguishing material, the FR Resin can 3D print strong, durable plastic parts that can withstand high temperatures. Formlabs Flame Retardant Resin used to make parts.

Let’s dive deeper into the details of each product and explore how they can enhance users’ 3D printing experience.
#Contact preform formlabs series
With these latest offerings, Formlabs is expanding the capabilities of its Form 3 series printers, bringing new options for printing materials, build platforms, and file formats to the table.Īnnounced at RAPID + TCT, the release of its first Flame Retardant Resin (FR Resin) for the Form 3 series printers, its new Build Platform 2L with Quick Release Technology for the Form 3L and Form 3BL printers, and PreForm support for 3MF (3D Manufacturing Format) files, are designed to offer unprecedented flexibility, speed, and accuracy for a wide range of 3D printing applications. Formlabs is shaking up the industry once again with the release of not one, but three new products.
